Quality & Inspection
Date:2019-09-27 Click:1105
All FLOWTEK Valves are inspected and tested at the factory as per procedures, that are in strict compliance with API and DIN/EN Specifications.
Inspections and Testing of FLOWTEK Cast Steel Valves are done as below.
1. Visual Examination
2. Hydrostatic shell test.
3. Backseat test.
4. Seat (water) test.
5. Low pressure (air) test.
6. Painting & packaging.
Cast Steel Valves are inspected and tested in detail as follows.
1. VISUAL EXAMINATION:
(Gate, Globe, Ball, Butterfly, Plug Valve, Strainer and Swing Check Valves)
A visual examination is performed on all casting of bodies, bonnets, covers and closure elements in accordance with MSS-SP-55, Quality Standards for Steel Castings and with reference to purchase specifications.
Marking inspection |
material & heat treatment report |
PMI |
wall-thickness inspection |
Dimension checking |
Dimension checking |
Dimension checking |
|
Dimension checking |
roughness checking |
roughness checking |
2. HYDROSTATIC SHELL TEST:
(Gate, Globe, Ball, Butterfly, Strainer and Swing Check Valve)
The purpose of this test is to ensure that the valve shell will withstand pressures up to 1.5 times of the working pressure at the 100°F for Body & 1.1 times for seat rating with no visual leakage or harmful in elastic deformation.

a) Frequency of Hydrostatic Shell Test
100% on all bodies.
b) Test Media
The test media is water containing a rust inhibitor at a temperature not exceeding 100 °F.
c) Test Pressure
The shell test pressure is 1.5 time of the design or working pressure rating of the valve, as per the standards.
VALVE RATING |
TEST PRESSURE (PSIG) |
Class 150 |
450 |
Class 300 |
1125 |
Class 600 (WCB) |
2225 |
Class 600 (Other than WCB) |
2250 |
d) Test Duration
VALVE NPS |
MIN. TEST DURATION (SEC) |
≤2 |
15 |
2-1/2”-6” |
60 |
8”-12” |
120 |
14” & ABOVE |
300 |
e) Test Procedures
The shell test is performed by partially opening the valve assuring that all internal surfaces seals and packing are exposed to the test media and apply pressure for the suitable time duration.
f) Acceptance / Rejection-criteria
No visible evidence of external leakage for the duration of the test.
3. BACKSEAT TEST
(Gate and Globe Valves only)
The purpose of the backseat test is to ensure that the stem backseat area will not leak at 1.1 times the pressure rating.
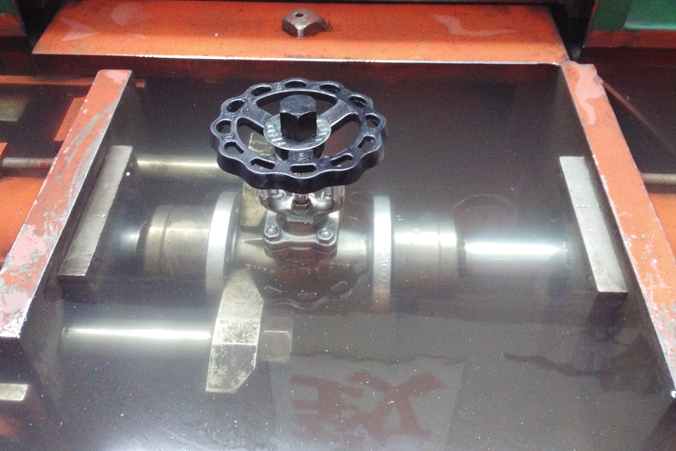
a) Frequency of Backseat Test
100% on all Gate and Globe Valves.
b) Test Media
The test media is water containing a rust inhibitor at a indoor temperature 0 - 25 ℃.
4. SEAT TEST (WATER)
(Gate, Globe, Ball, Butterfly and Swing Check Valves)
The purpose of the seat test is to ensure that the sealing area will not leak at 1.1 times the pressure rating.
a) Frequency of seat Test
100% on all shuf-off valves (Gate, Globe, Ball, Butterfly and Swing Check Valves)
b) Test Media
The test media is water containing a rust inhibitor at a indoor temperature 0 - 25 ℃.
c) Test Pressure
The seat test pressure is 1.1 time of the design or working pressure rating of the valve, as per the standards.
VALVE RATING |
TEST PRESSURE (bar) |
Class 150 |
22 |
Class 300 |
55 |
Class 600 |
110 |
Class 900 |
165 |
Class 1500 |
275 |
d) Test Duration
VALVE NPS |
MIN. TEST DURATION (SEC) |
≤2 |
15 |
2-1/2”-6” |
60 |
8”-12” |
120 |
14” & LARGER |
300 |
e) Test Procedures
The seat test is performed by completely closed the valve, the water is fully in the upstream port, then check the sealing area on downstream side. For the bi-directional valves, the test shall be performed again from the other side.
f) Acceptance / Rejection-criteria
No visible evidence of leakage for the duration of the test.
5. LOW PRESSURE (AIR) TEST
(Gate, Globe, Ball, Butterfly, Plug valves)
The purpose of the low pressure test is to ensure that the sealing area will not leak at 0.6 MPa (6 bar) air pressure.
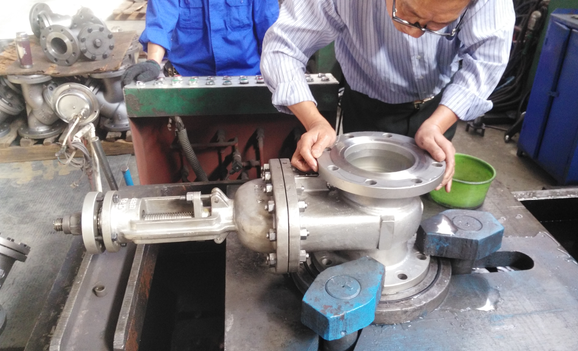
a) Acceptance / Rejection-criteria
No bubble for the duration of the test (EN12266-1 Class A zero leakage / API6D Class A zero leakage).
6. LOW PRESSURE (AIR) TEST
a) Painting.
RAL 5015 top color |
special primer painting for high temperature 600 deg.C |
Silver color RAL 9006 or 9007 |
Ready for packaging |
b) Packaging.
Very strong packing for different kind of valves.
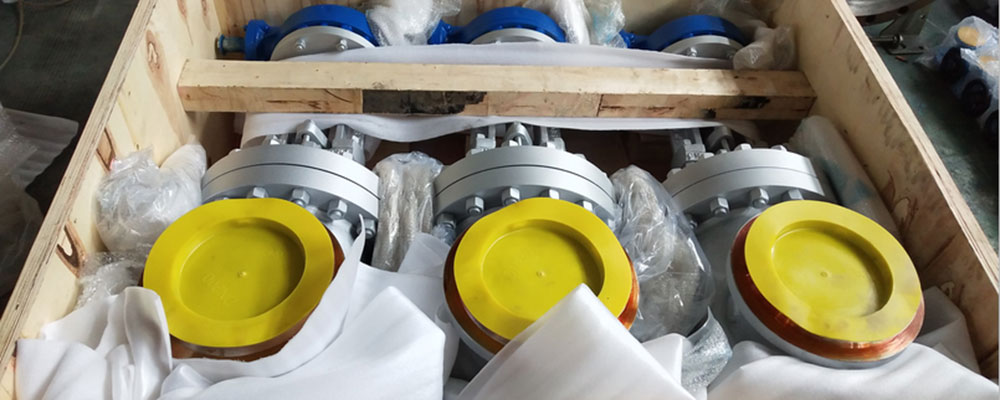
Seaworthy plywood box packing suitable for export